Formulating a production plan
The production supervisor devises weekly plans based on sales orders and issues production instructions.
Procure and inspect raw materials according to the production plan.
To ensure product quality, we select suppliers that are fully qualified and have a certain scale of production. Upon arrival of raw materials, we immediately inspect their quality and corresponding quality inspection reports to ensure that only qualified materials enter the production process.
-
Fabric quality inspection1
-
Fabric quality inspection2
Mattress cover production
Firstly, we strictly adhere to the cutting requirements of the drawings. We have computerized automatic cutting beds to ensure that all product dimensions are within reasonable tolerance ranges, while also maintaining production efficiency.
After cutting, dedicated personnel inspect the fabric for size and appearance to ensure it meets standards. Materials that meet all criteria proceed to sewing or heat sealing according to the order requirements. Our seamstresses and heat sealers have years of experience to ensure perfect product delivery.
-
Fully automated cutting and production
-
Heat sealing process
-
Sewing process
Mattress core production
According to different orders, we have various options including pure sponge, sponge with cotton, and sponge with airbags or gel. For sponge cutting, we use 3D CNC cutting machines, specialized eggshell slitting machines, manually adjustable vertical cutting machines, and high-speed punching closed-loop systems to meet different order requirements, such as tofu blocks, wave shapes, and other irregular shapes.
-
3D CNC cutting
-
Eggshell dedicated slitting machine
-
Manually adjust the vertical cutting machine
-
High-speed punching closed-loop cutting
-
Various Alien Requirements
High-speed punching closed-loop cutting
According to the order requirements, insert the mattress core into the corresponding mattress cover, ensuring that the mattress surface is smooth and standardized.
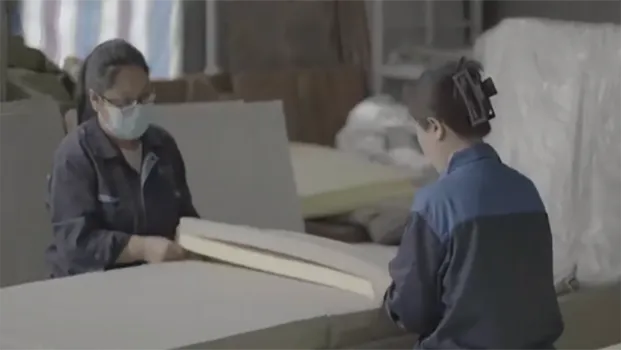
Fabric quality inspection
Finished product inspection
According to the order requirements, inspect the mattress cover and mattress core to ensure they are made according to the drawing specifications, including dimensions, colors, details, etc.
-
Verify the orde
-
Dimension measurement
-
Outerwear detail inspection
-
Foam detail inspection
Goods loaded and dispatched